Injection Molding Design: Things to Consider
Plastic injection molding is a versatile, powerful, cost-effective technique for rapidly creating products for dozens of industries. Ensuring a mold design that will work best with your chosen plastic material will produce the best results with this speedy, accurate process. Some things to keep in mind when designing your mold include:
Movement through the Mold
Fundamental to the whole molding process is how the injected plastic resin will move through the mold. Areas where it moves slowly, unevenly, or incompletely, can result in poor quality and appearance. Consider:
Wall Thickness
Mold designs should allow melted plastic to move from thicker areas to thinner areas to avoid creating a bottleneck and possibly blockages if the plastic cools and solidifies too quickly.
Crevices and Hollow Spaces
Forcing the flow of melted plastic into hollow areas or crevices can be challenging for injection molding. Limiting such spaces in your mold design can improve quality and allow for a more cost-effecting molding process.
Angles and Curves
If you envision the melted plastic flowing into the mold, you can imagine that sharp angles can slow or block the flow while curves and gentle angles can move it along smoothly.
Level of Detail
Injection molding allows for a high level of both detail and accuracy. Though molding costs may be a little higher, production costs will be lower, and high accuracy is maintained over even very extended production runs.
Material Selection
Each type of plastic resin will flow through a mold and cool differently, so choosing compatible materials and mold designs is vital for successful results.
Mold Ejection
At the end of each cycle, the finished part must be ejected from the mold. Simple, single-step mold ejection will be the most efficient and cost-effective design, while additional steps will add to your bottom line.
Recent Articles
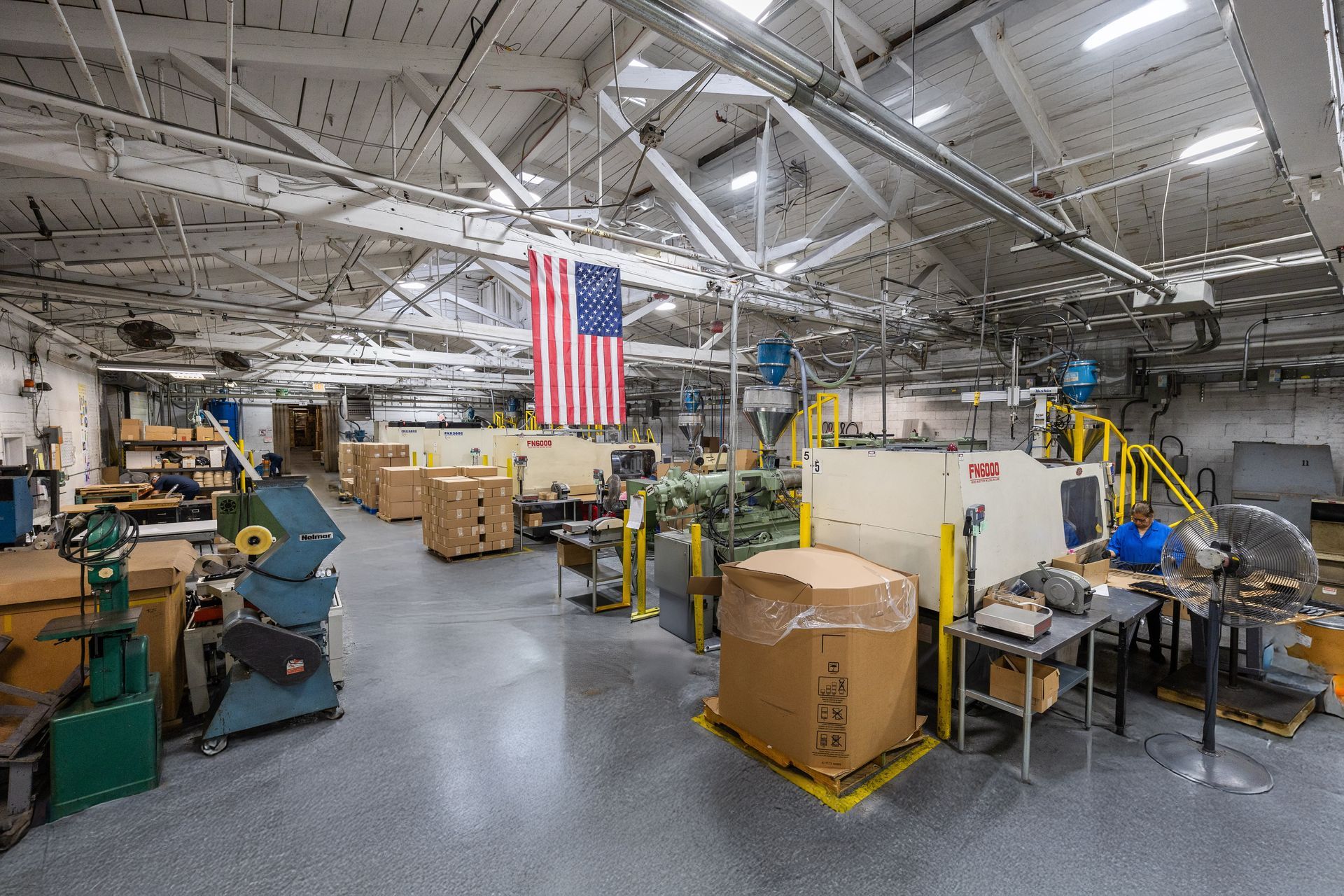
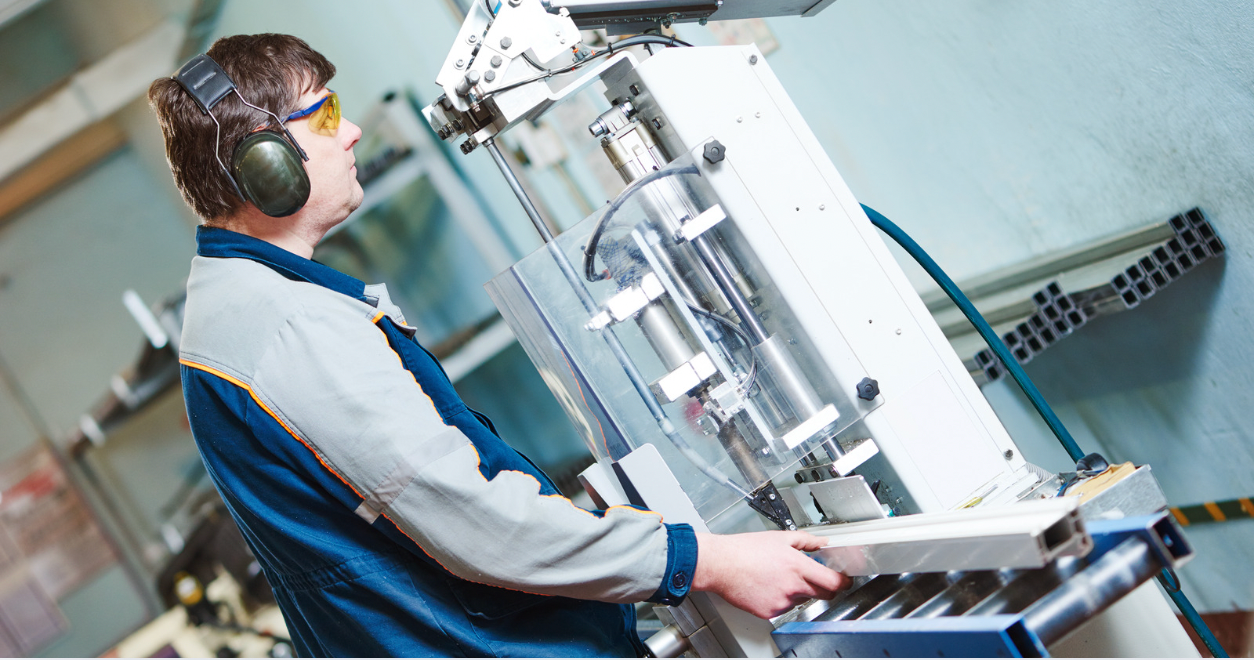
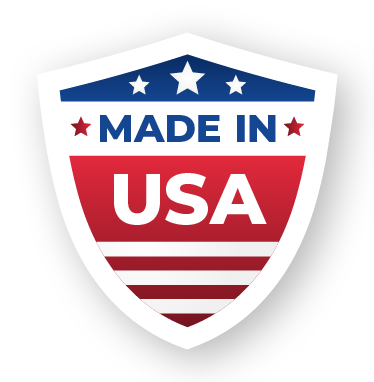