4 Helpful WaysTips to Prevent Defects in Common Plastic Injections
When it comes to plastic injection molding, there's room for several errors. Quality issues in plastic injection-molded items range from negligible surface defects to severe problems that affect the performance, safety, as well as function of the final product. Often times, the flaws are linked to the material used, tooling design, molding process, or a combination of all three.
Injection Speeds
Lowering resin injection speeds is proven to significantly lower burn marks. Burn marks are typically surface marks caused by resin that overheats or overheated trapped air. Decreasing resin injection speeds lowers the possibility of air becoming trapped, optimizes degassing and venting systems, and also reduces the mold/melt temperature.
Material Selection
Selecting the right material enhances the versatility and functionality of your product. It is advisable to work with a well-informed injection molder and design engineer to learn how various materials can optimize the life of your plastic part. The material selection is usually centered on the application of the product. The plastic requirements for food industry products may be immensely different than those of medical applications.
Processing Parameters
There are circumstances where the color of the finished product is different than the projected. This fault is usually caused by scorching barrel temperature, leftover pellets in the hopper, or unused resin in the feed zone. To prevent discoloration of the final product, it is advisable to flush the feed and hopper zone of the processing machine in between processes.
Tool Design and Build
A defect-free, flawless part starts with the mold. Designing and producing a product represents the largest investment in most manufacturing processes; thus, getting it right from the word go is vital to the success of the injection molding project. The material and volume of parts needed are of significant help when creating a mold.
Let Bennett Plastics Help!
The best way to prevent injection molding defects is to work with a knowledgeable service provider that fully understands the characteristics of multiple resins and their applications.
Contact us today to learn how Bennett Plastics can help you lower injection molding defects. With over 30 years of experience, we have the expertise and equipment to bring your design dreams to life.
Recent Articles
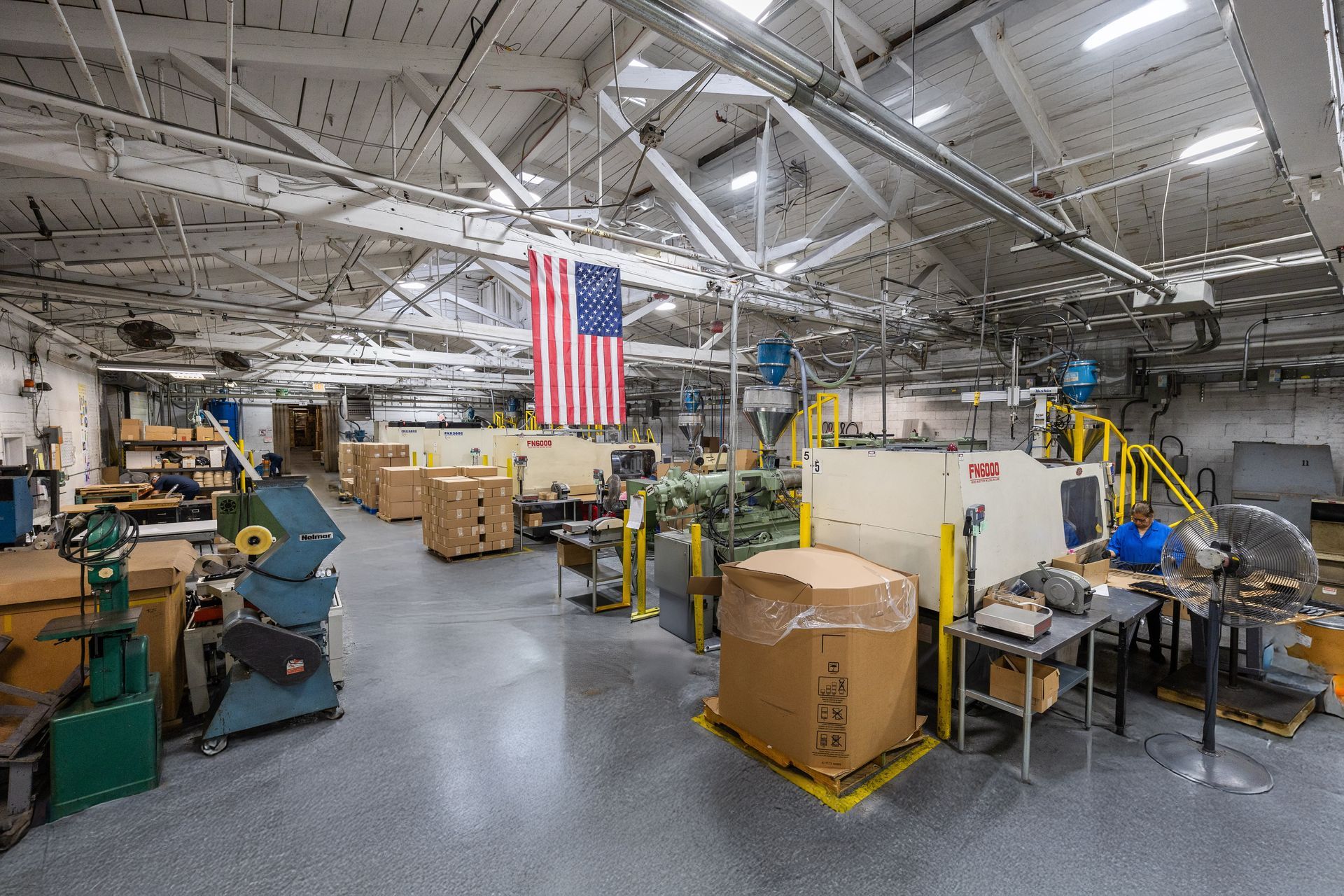
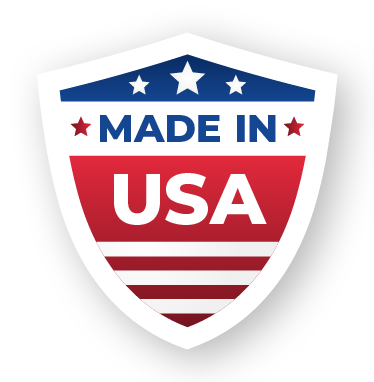
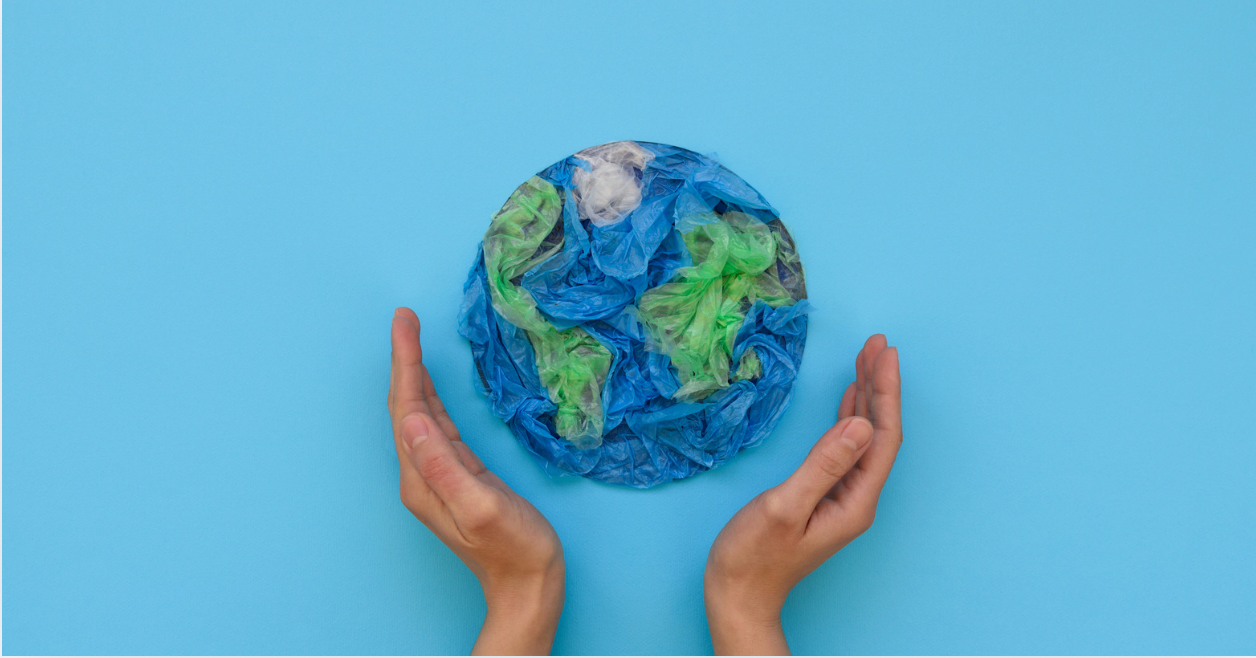