The Pros and Cons of Custom Plastic Molding
What Is Custom Plastic Molding?
Custom plastic injection molding involves the creation of a unique mold and selection of materials to produce a specific part or product that meets your precise specifications and requirements. Unlike other industrial fabrication processes, custom plastic injection molding offers an array of benefits and only a few disadvantages which can be easily overcome with a little careful planning.
Pros:
Speed of Production
After the initial setup, plastic injection molding is an automated, rapid process, allowing many products and parts to travel through the full production cycle in a matter of seconds.
High-quality, High-strength Products
Many plastic formulations and blends can be as strong as metal, and the injection molding process lends itself to consistent, accurate production of parts in volume.
Cost-effectiveness
Because the plastic injection molding process is primarily automated after initial setup, labor costs are low, saving you money.
High Accuracy & Repeatability
Plastic injection molding can produce parts with accuracy as fine as .005 inches. It is also a very consistent, repeatable manufacturing process, increasing part reliability.
Versatility
Combinations of shapes, materials, additives, colors, details, and finishes that injection molded plastics offer are nearly endless, allowing exceptional versatility.
Efficiency
With little, if any, finishing required, injection molding makes excellent use of manufacturing time. Additionally, scrap can be recycled and reused for greater material efficiency.
Sustainability
Options for eco-friendly plastics and renewable materials in our environmentally-conscious facility ensure production is as sustainable as possible.
Design Flexibility
The specific nature of the plastic injection molding process offers opportunities for nearly endless designs and shapes.
Cons:
Initial Costs
Mold tooling costs can be high, and are usually the greatest expense in manufacturing an injection molded plastic product.
Potentially Longer Lead Time
Because prototyping and tooling must be done accurately and carefully, lead time may be longer than you may have initially expected.
Modifications
Because molds are typically made from steel, later-stage modifications may be difficult, time-consuming, or costly to make.
Technical Considerations Influencing Design
The injection molding process, while very versatile and flexible, does have some limitations in what is technically possible to produce. These limitations may, in a few cases, affect product designs.
Taking advantage of the expertise and experience of a skilled design and production team, such as the team we have here at Bennett Plastics can mitigate most of these disadvantages. We work together, in-house, and take great care to do it right the first time so your tooling and prototyping costs and time are as low as possible while maintaining our commitment to superior quality.
Contact us today to learn more about our custom plastic injection molding capabilities.
Recent Articles
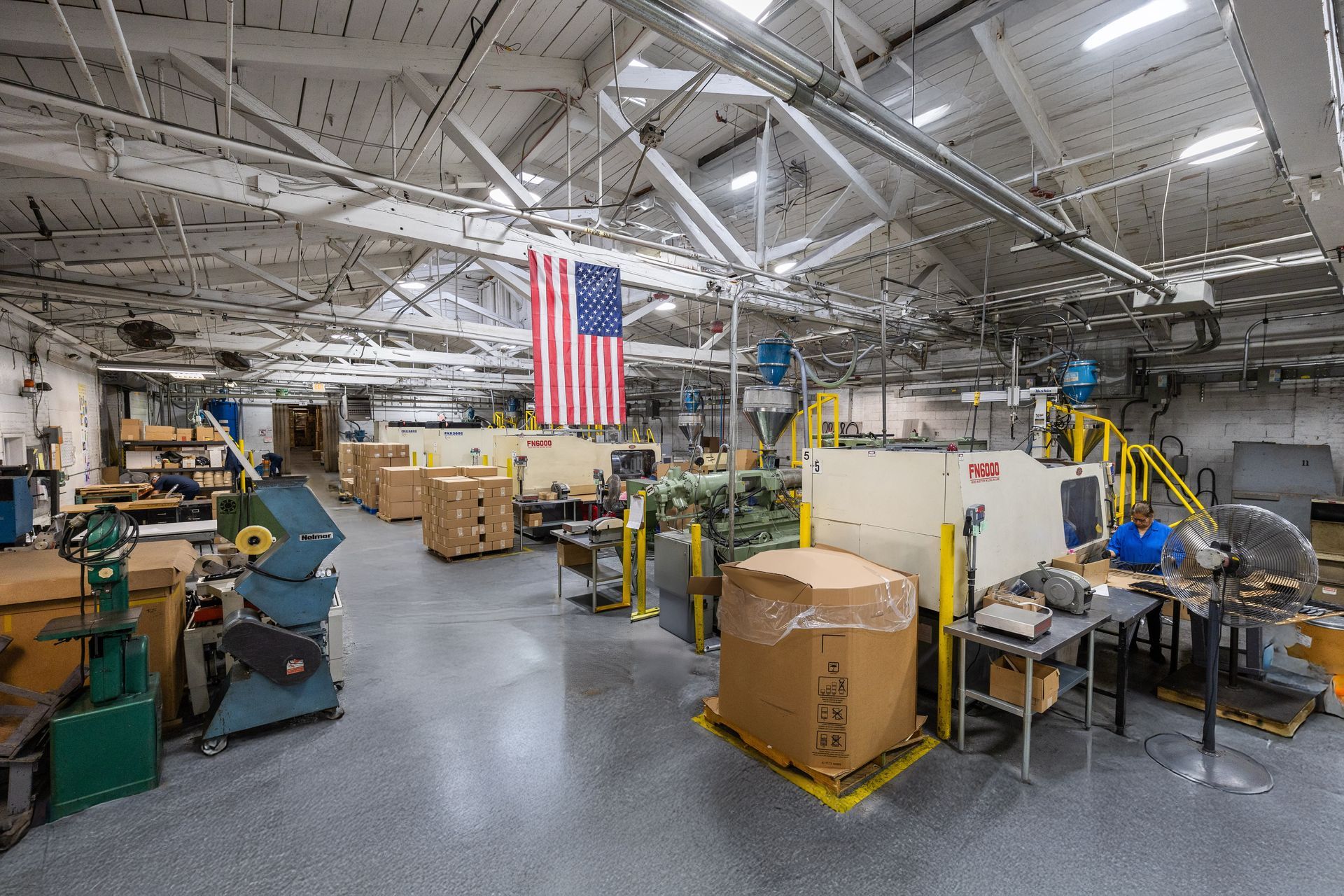
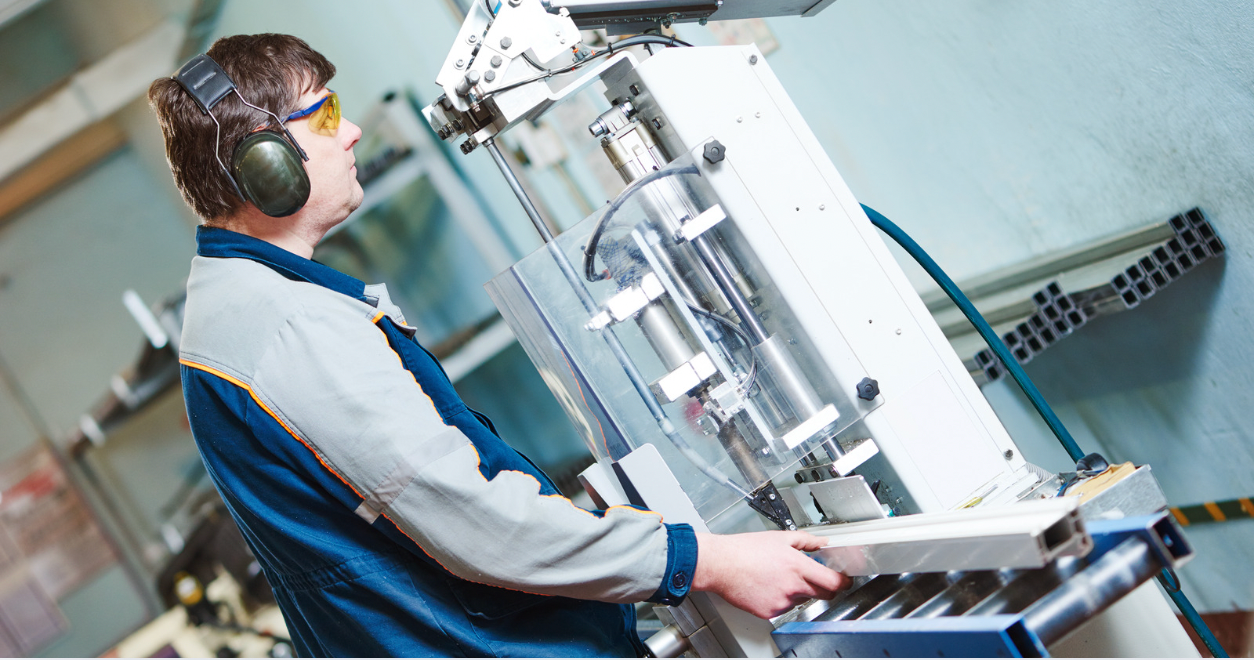
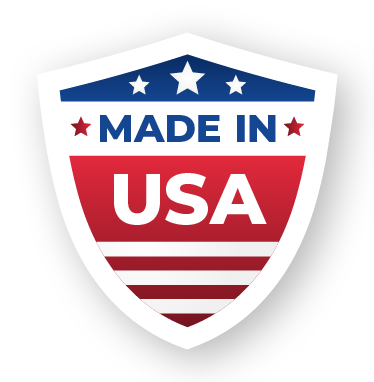