How a Prototype Will Save You Time and Money
Since prehistoric peoples advanced from using rocks to shaping tools out of copper and iron, metal and wood have been the favorites for making nearly any parts and components. Even well into the 20th century, most plastics were too weak or brittle to take the place of metal parts. Today, custom plastics manufacturing can take advantage of innovative plastic formulations that can meet or exceed metal's performance.
Advantages of Plastic Parts Over Metal Parts
Especially when the idea of replacing metal parts with plastic ones was first being explored, many scoffed at the very idea of flimsy plastic replacing powerful metals. Chemists, engineers, and the entire plastics industry have worked to create plastic formulations that can rival or outperform metal for the same use. Today, many industries consistently prefer plastic parts over metal ones.
Plastic Parts Can Be Stronger Than Metal
Modern plastics, especially with the addition of carbon or glass fibers, can be extremely strong and durable. The natural flexibility of plastic can also make these strong parts a little more resilient than metal.
Plastic Is More Resistant Than Metal
Plastic is better suited to withstanding all sorts of hazards and exposures, including moisture, chemicals, electrical current, and abrasions. Even heat-resistant resins are available.
Plastic Provides More Variety & Customization
Whether you need more flexibility in your design, a variety of colors, textures, or other characteristics, plastic parts are easily customized. Changes can also be made during production, and multiple resins can be used.
Plastic Parts Are Less Expensive to Make
Using plastic parts instead of metal ones can save your budget, with reduced costs for:
- Raw materials
- Minimal waste and smaller carbon footprint
- Little if any secondary steps or finishing needed
- Transportation due to lighter weight of parts
Plastic Parts Offer Faster Production
Injection molding is incredibly fast, and consistent over even very long production runs.
At Bennett Plastics, we can help you convert your metal parts to plastic ones, or work with you to design new plastic parts to meet your needs. Contact us today to partner with our full-service team of experts.
Recent Articles
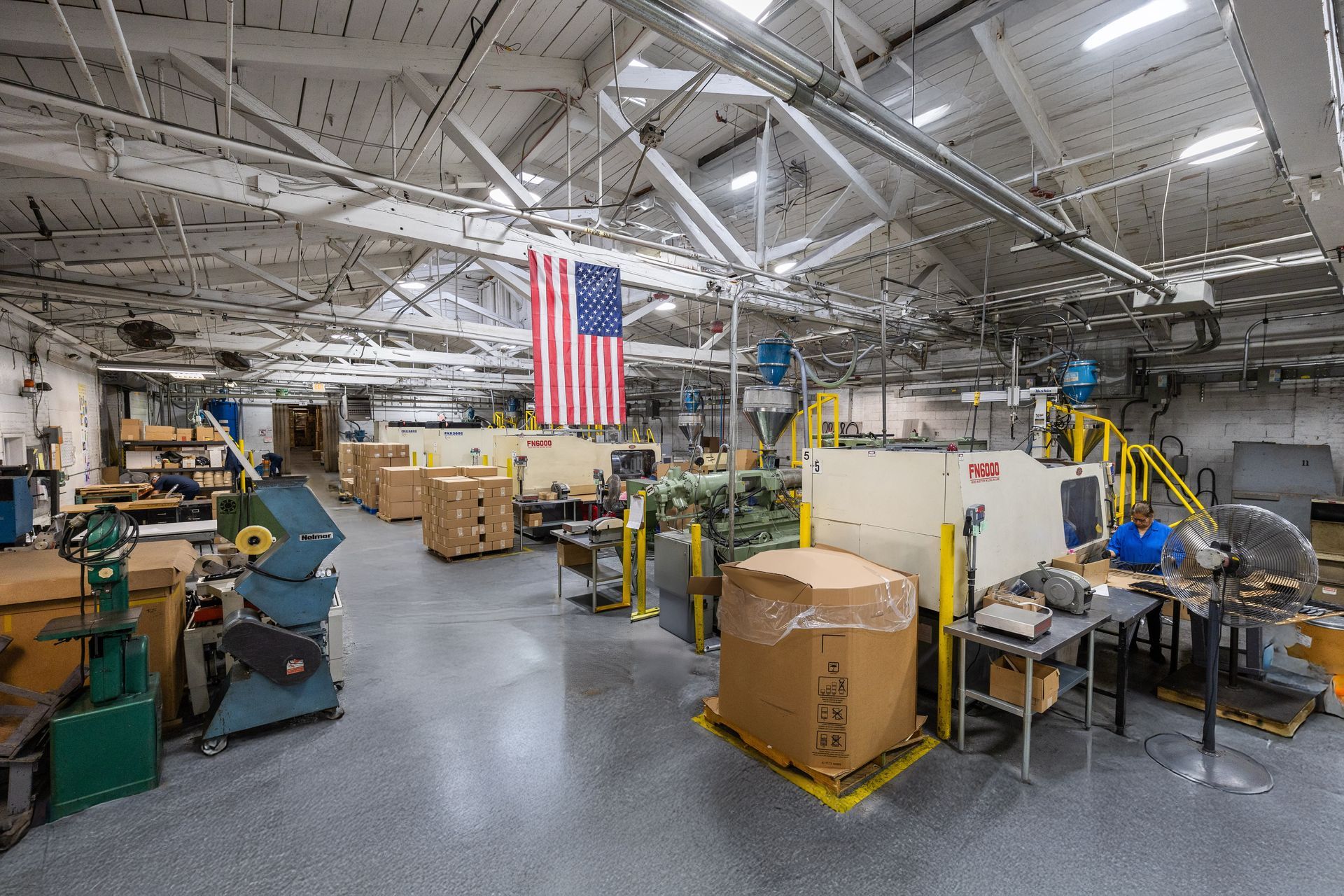
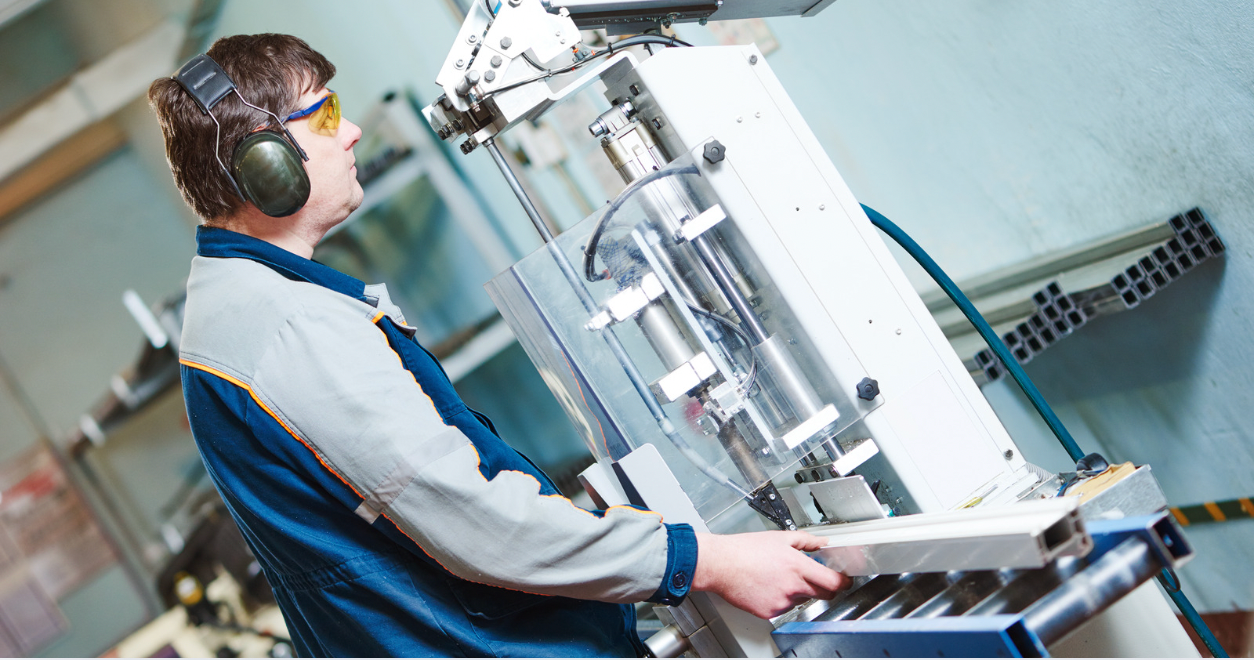
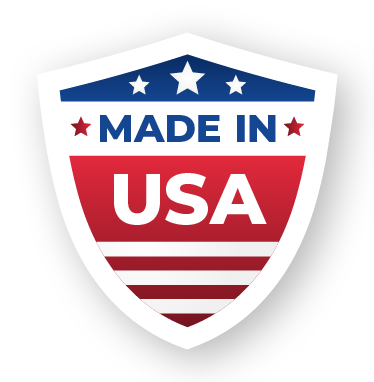