The 6 Main Steps of Plastic Injection Molding
The process of plastic injection molding truly starts with part and mold design, polymer selection, and prototyping to ensure a top-quality result. While these preliminary but critical stages may take a few weeks, the actual injection molding process is so efficient, many parts can be fully molded in mere seconds. Here's how it works.
Closing the Mold
Whether preparing for the initial molding cycle or after ejecting the previously molded part, the first step is to close the mold so that all openings are blocked except the gate (to allow melted plastic to enter the mold), the mold cavity (where the actual part is molded), and tiny vents which allow the air flow needed for successful molding.
Injecting Polymer
A barrel with an auger or screw inside is filled with pellets of the selected polymer resin. As the auger turns, the pellets move from the feeder area into a zone where the barrel is heated to melt the resin to a specified temperature. As the auger moves forward, melted polymer resin is forced at high pressure into the mold, displacing the air inside, which escapes through the tiny vents.
Cooling
Naturally, the melted plastic must cool and harden in the mold in order to retain its shape. Molds are designed with channels to allow a coolant, normally water and/or ethylene glycol, to flow through and cool the mold and the part inside it at a carefully determined rate.
Reloading the Barrel
When the part is cooled, the auger moves back and the barrel is reloaded with additional polymer pellets to prepare for the next cycle.
Ejection
While the pellets are heating, the mold opens and the cooled part is removed from the mold by ejector pins which push it away from the mold surface where it drops into a box, chute or conveyor system.
QA & Finishing
Finally, parts are checked to ensure they meet our high standards, and any finishing steps are performed, such as removing any rough edges left where the mold halves meet.
At Bennett Plastics, we have decades of experience and expertise with every step in the plastic injection molding process. Contact us today to learn more about our capabilities and our array of value-added services.
Recent Articles
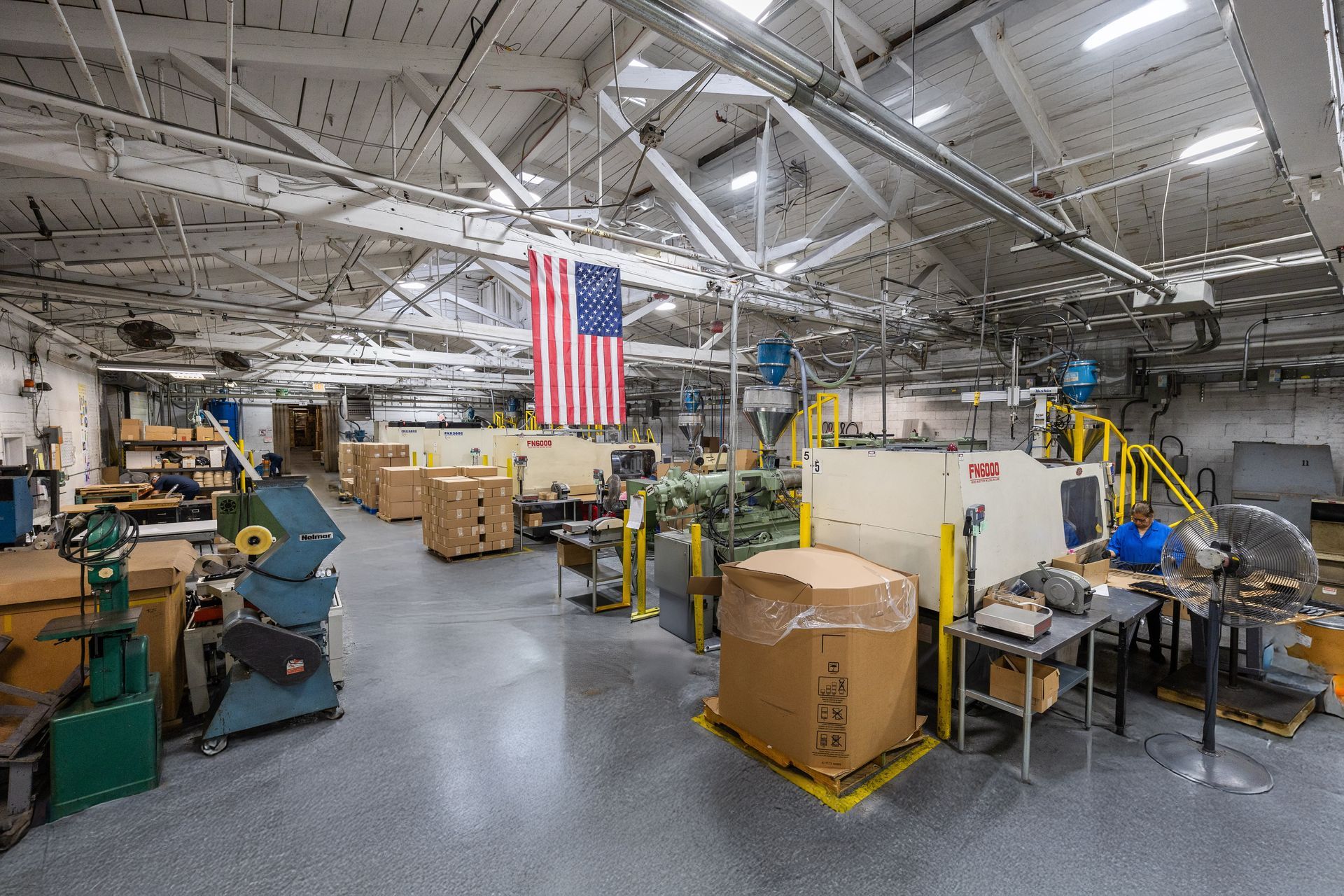
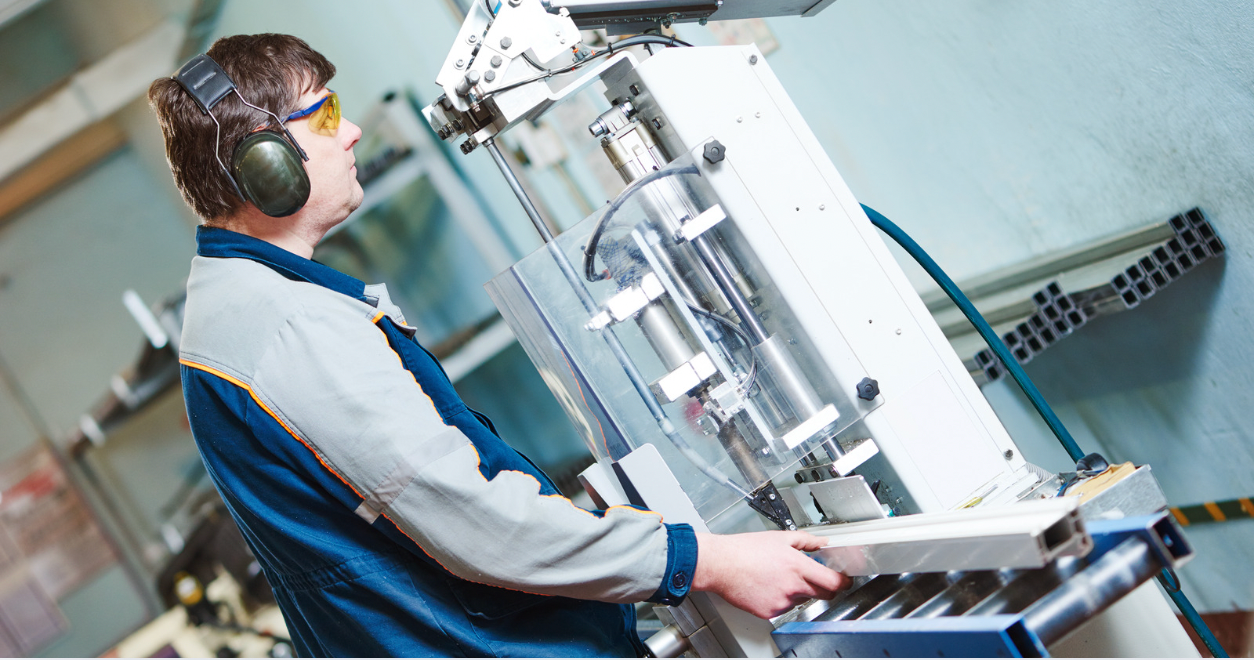
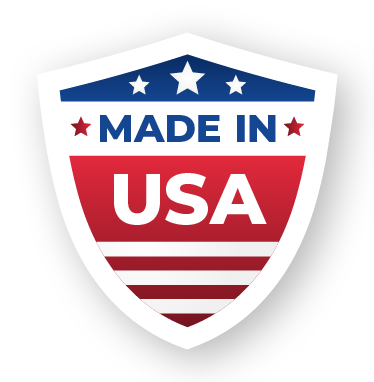