5 Tips for Designing Injection Molded Plastic Parts
5 Helpful Design Tips for Injection Molded Plastic
Designing a part for manufacturing is a crucial component of getting a product to market, and designing that part for plastic injection molding requires some special considerations. Here are five tips for designing the perfect part.
Prototypes
Creating a prototype is an essential part of the part design process, particularly for injection molding. An early prototype can save on costs by helping to identify potential problem areas for the flow of plastic through the mold, cooling without warping or sinking, and possible ejection issues. Prototypes also allow you to physically examine and test a part before taking the next step to full-scale production.
Mold and Part Interaction
The simplest and most cost-effective design will allow parts to be molded with a simple open-and-close action of the mold rather than more complex (and more expensive) side action or lifting mold mechanisms.
Plastic Flow
- Thick to Thin - A critical part of planning any part for plastic injection molding is to take into consideration the way plastic will flow through the mold. You want to make sure it will flow through rapidly, smoothly, and evenly. The best designs will force plastic to start in the thickest areas and progress to thinner areas which helps prevent blockages if plastic cools too quickly in thin areas preventing material from reaching the areas beyond that point.
- Wall Thickness - Consistent wall thickness for best flow will aid in the smoothest flow of plastic and will help prevent warping and unattractive sinks during the cooling process.
- Curves - Rounded corners and smooth transitions rather than sharp angles and corners will keep the plastic flowing easily through the mold, helping to reduce stress on the plastic and prevent warping and weakness.
Mold Ejection
Getting your part out of the mold after it's cooled is just as important as getting the plastic properly into the mold in the first place. Adding an appropriate taper (draft angle) to parts will make them less likely to stick in the mold, and will add to the stability of parts. Rough surfaces for parts can also make them difficult to eject from molds.
Materials
The types of plastics used for parts should be carefully chosen. Each kind of polymer, additive, and filler has different suitabilities for different types of parts. For the best results, take into consideration the stress and strains on the part, the strength it will need, its durability and lifespan, the cost of different material choices, and, of course, its physical appearance.
There's a lot to take into account when designing a part for plastic injection molding. Bennett Plastics has decades of experience in successfully taking customers through the entire process, from prototype design to finished products. Contact us today to see how we can partner with you to bring your product to life.
Recent Articles
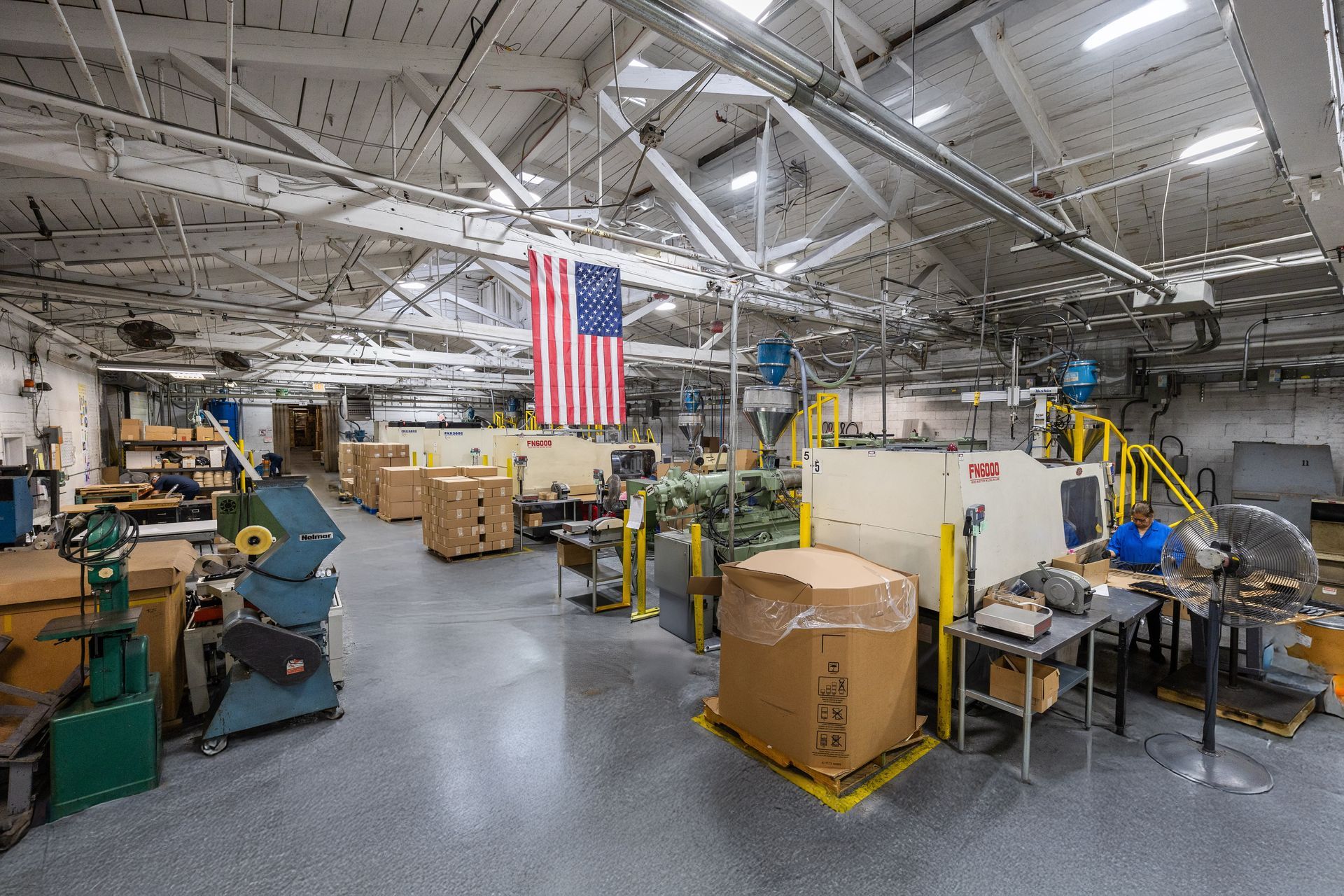
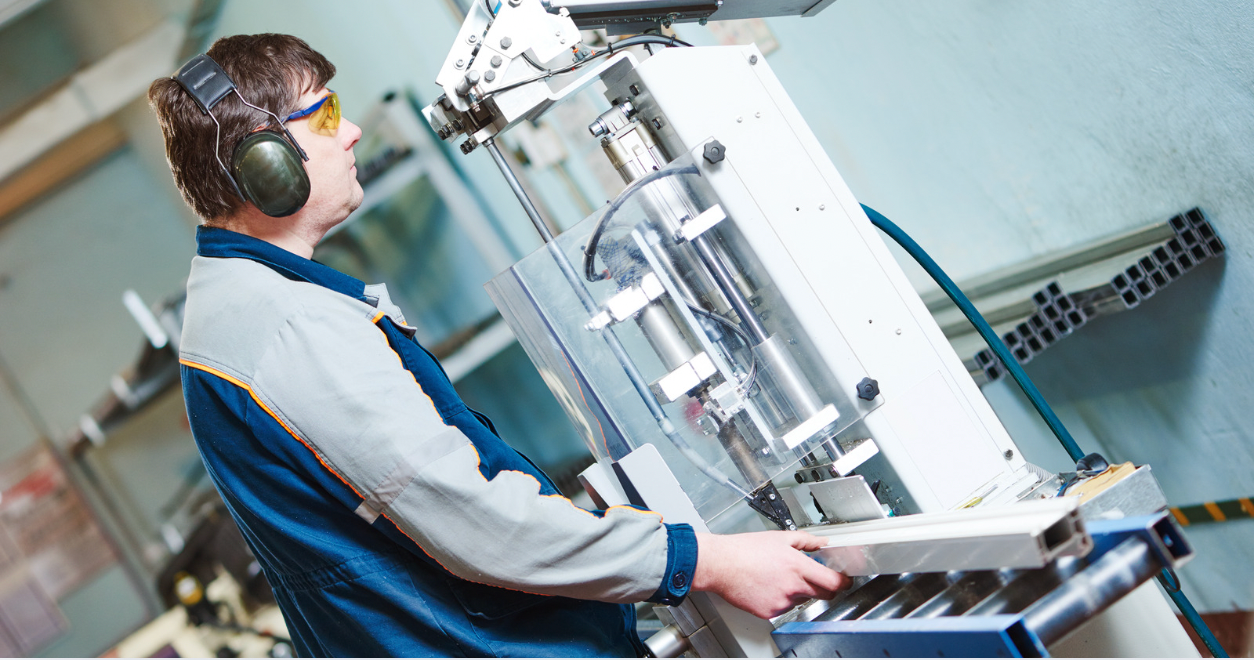
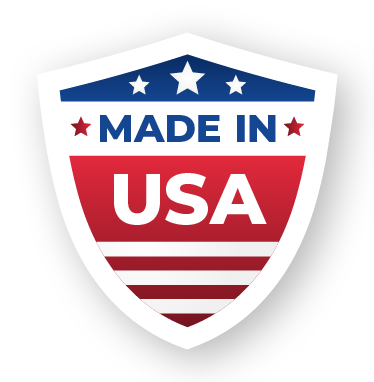